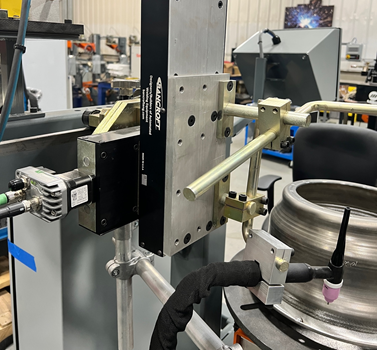
As technology continues to advance, automated welding processes are becoming more prevalent in industries such as automotive, aerospace, and manufacturing. Among these processes, Gas Tungsten Arc Welding (GTAW), commonly known as Tungsten Inert Gas (TIG) welding, is highly regarded for its precision and quality. However, like any welding process, automated GTAW welding also presents its own set of challenges. In this blog, we will explore some of the common challenges associated with automated GTAW welding and discuss potential solutions to overcome them.
Â
Challenge 1: Precise Control of Welding Parameters
One of the critical aspects of automated GTAW welding is maintaining precise control over welding parameters, such as arc length, voltage, amperage, travel speed, WFS, and heat input. Any deviation from the optimal parameters can result in weld defects, such as lack of fusion, porosity, or incomplete penetration. Achieving consistent and precise control over welding parameters can be challenging due to factors such as material variations, joint fit-up, and changing welding positions.
Â
Solution: Advanced Welding Automation Technology
To overcome this challenge, investing in advanced welding automation technology is crucial. Modern automated welding systems often come equipped with advanced features such as closed-loop control, real-time monitoring, and adaptive welding techniques. These technologies allow for precise control and monitoring of welding parameters throughout the welding process, ensuring consistent and high-quality welds. Additionally, using sensors, cameras, and feedback systems can provide real-time data, enabling adjustments to be made in real-time, resulting in improved welding accuracy and efficiency.
Â
Challenge 2: Joint Fit-Up and Alignment
Achieving proper joint fit-up and alignment is crucial for successful GTAW welding. In automated welding, the joint fit-up and alignment can vary due to factors such as tolerances in parts, variations in material thickness, and fixture inaccuracies. Poor joint fit-up and alignment can lead to uneven heat distribution, lack of fusion, and distortion in the final weld.
Credit : Source Post