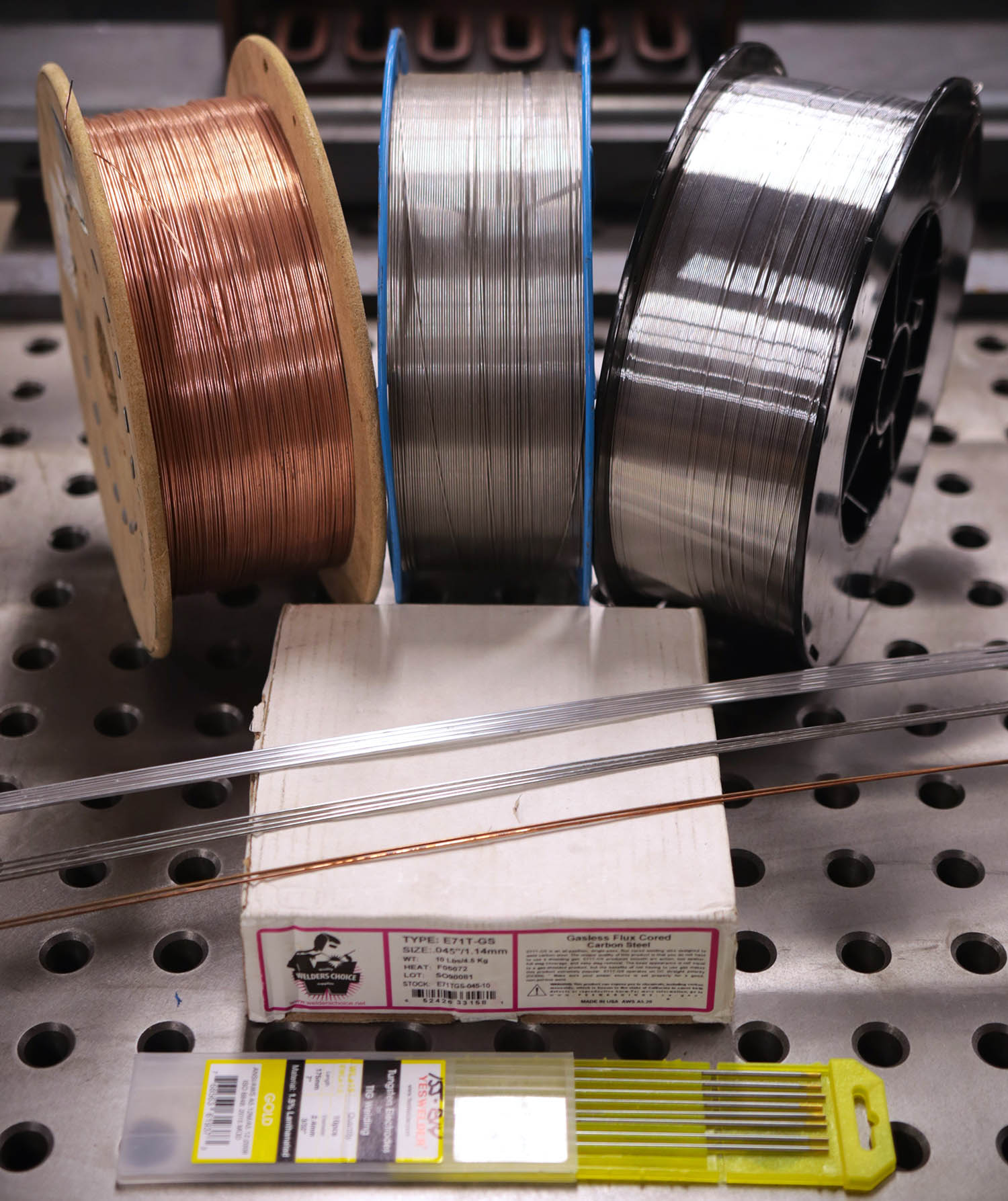
Welding is a critical process in the world of metal fabrication, and it plays a pivotal role in the success of various industries! When it comes to welding—whether you’re manually welding or using an automated solution—one of the key factors that significantly influences the quality and durability of the end result is the choice of filler metal.
We understand the significance of selecting suitable filler metal based on material conditions. In this welder’s guide, we will examine all of the considerations and factors involved in making such an important decision.
Â
The Significance of Filler Metal SelectionÂ
Filler metals are essential components in automated & manual welding that are used to join two base metals. They come in various forms, such as wires, rods, and powders—each designed for specific welding processes and materials.
Selecting the appropriate filler metal is crucial because it directly impacts the strength, corrosion resistance, and other mechanical properties of the final weld. The wrong choice can lead to defects, weakened welds, and quality check failures.
Â
Factors Influencing Filler Metal Selection
#1. Base Metal Type: Different metals and alloys require specific filler metals. The compatibility of the filler metal with the base material is paramount for a successful weld.
#2. Base Metal Condition: Consider the condition of the base metal, including its cleanliness, thickness, and any pre-existing defects or corrosion. Some filler metals are better suited for addressing such conditions.
#3. Welding Process: Various welding processes, such as MIG (Metal Inert Gas), TIG (Tungsten Inert Gas), and stick welding, require different filler metals. The choice of filler metal should align with the welding process being used for the project.
#4. Welding Position: The welding position (ie: flat, horizontal, vertical, overhead, etc.) can affect the flow and behavior of the filler metal. Certain filler metals are better suited for specific positions. Learn about our array of welding positioners right here.
#5. Mechanical Properties: Consider the desired mechanical properties of the weld, such as tensile strength, ductility, and hardness. Some filler metals offer better performance in these areas than others.
#6. Corrosion Resistance: In applications where corrosion resistance is critical, (such as parts for the marine, aerospace, automotive & food processing industries) choosing a filler metal with the right alloying elements can prevent premature degradation of the weld.
#7. Welding Environment: The environment, including temperature and exposure to chemicals, can impact the choice of filler metal. For example, high-temperature applications will require filler metals with excellent heat resistance.
#8. Cost Considerations: Your budget constraints may play a part in selecting filler metal, but it’s important to balance cost-effectiveness with project requirements as your welds may suffer.
The choice of filler metal in welding is a critical decision that directly impacts the integrity and longevity of your welds. We understand the importance of this choice and leverage our expertise to ensure your welding projects & equipment are a success. By considering the factors mentioned in this guide and collaborating with experienced professionals, you can make informed decisions that lead to superior welds and reliable finished components.
Â
Bancroft Engineering’s Expertise
Bancroft Engineering provides top-tier automated welding systems and equipment that have revolutionized manufacturing processes. Our cutting-edge technology is optimized for productivity and efficiency—specializing in weld lathes, seamers, rotary welders, automatic positioners, custom solutions, and so much more.
Our history of innovation in welding technology spans decades, and we remain committed to offering top-quality solutions & equipment at competitive rates. Experience the Bancroft difference in automation today and expand your manufacturing capacities!
Credit : Source Post